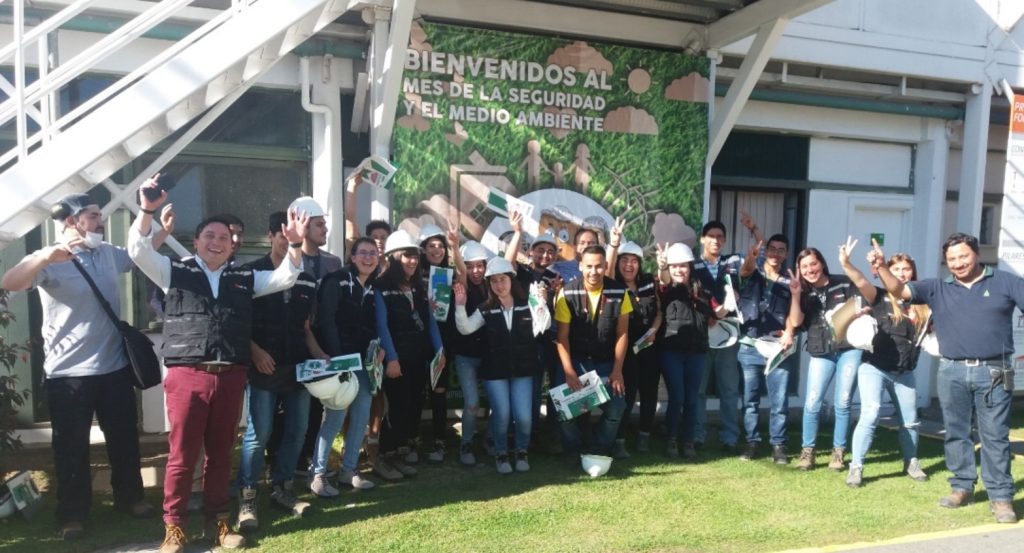
En cada unidad de negocio y filiales de CMPC se genera un total de 1.8 MM Ton de residuos, los que tienen formas diferentes de disposición, dependiendo del tipo de material y su condición de peligrosos o no; 0,7% y 99,3% del total, respectivamente.
Los residuos se disponen a través de los siguientes modos: compostaje, reciclaje, recuperación, reutilización, valorización energética, venta a terceros, disposición final y vertederos. Para Celulosa, aplican todos los modos, salvo reutilización; para Biopackaging, exceptuando venta a terceros; y Softys, salvo compostaje, recuperación, valorización energética, venta a terceros y vertederos.
En esta línea, a 2025, CMPC se ha propuesto ser una compañía Cero Residuos, reduciendo la generación de residuos, valorizando sub-productos y fortaleciendo modelos circulares. Para esto, desde 2010, Celulosa, en conjunto con la Universidad de Concepción, realiza estudios para utilizar el lodo de cal y efluentes, de dregs & grits y cenizas de biomasa, residuos sólidos del proceso de fabricación de celulosa – hasta ese momento – sin uso productivo. En 2013, la mayoría de los residuos sólidos del proceso de fabricación de celulosa fueron clasificados como “subproductos” por resolución de la autoridad ambiental para las 3 plantas de CMPC Pulp, contando con los permisos ambientales para darles otros usos.
Otro ejemplo de esta transformación son las plantas de Softys ubicadas en Colombia, Gachancipá (tissue) y Santander (sanitarios), las que reprocesan el 100% de sus residuos de lodo papelero. El primer paso para lograrlo fue definir los tipos de residuos que se generaban, para luego buscar metodologías de disposición diferentes al relleno sanitario, usando los deshechos en sub productos o materias primas. En Gachancipá, el lodo se usa para fabricación de ladrillos arquitectónicos, material mejorado en su cocción, con lo que se reduce el consumo de arcilla y peso del ladrillo. Además, se genera compost para los agricultores de la zona que lo utilizan para mejorar sus cultivos. En Santander, a través de terceros, se logra reprocesar los lodos transformándolos en dispositivos SAP (Polímero Súper Absorbente, por sus siglas en inglés) y celulosa para liberación gradual de abonos para cultivos.
La planta de Guaíba, en Brasil, recicla el 99,7% de residuos del proceso de fabricación de celulosa. Los materiales sobrantes, como fibras de madera, hemicelulosas -entre otros- son transformados en abono y fertilizantes orgánicos para la producción agrícola.
Finalmente, Forsac, Envases Impresos, Chimolsa y Sorepa (filiales de Biopackaging) han firmado Acuerdos de Producción Limpia (APL) de Envases y Embalajes, apuntando a la reducción y optimización de residuos.
Resultados cuantitativos: